Bamboo pellet machines have become increasingly popular in the biomass energy sector due to their ability to convert bamboo, a renewable resource, into high-energy pellets. The efficiency of these machines is influenced not only by their design and operation but also significantly by the choice of accessories used in the production process. This article explores how selecting the right accessories can enhance the production efficiency of bamboo pellet machines and ultimately improve the quality of the final product.
1. Understanding the Role of Accessories
Accessories in a bamboo pellet production line include various components that support the main pelletizing process. These can include:
- Feeders: Devices that regulate the flow of raw materials into the pellet machine.
- Crushers: Equipment used to reduce the size of bamboo before it is processed into pellets.
- Conditioners: Machines that add moisture and heat to the raw material, preparing it for pelleting.
- Cooling Systems: Equipment designed to cool the pellets after they are formed, ensuring they maintain their shape and quality.
- Packaging Machines: Systems used for packaging the finished pellets for storage or distribution.
Each of these accessories plays a critical role in the overall efficiency of the pellet production process.
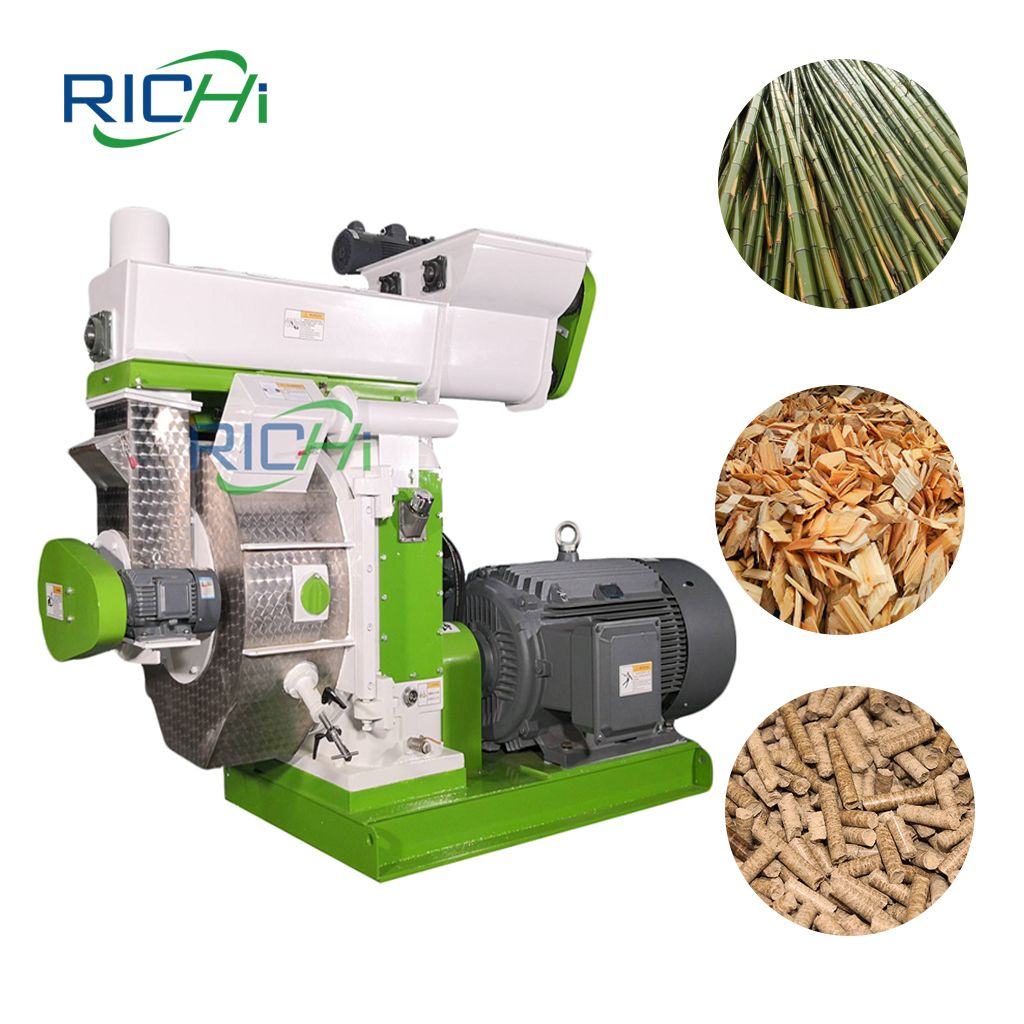
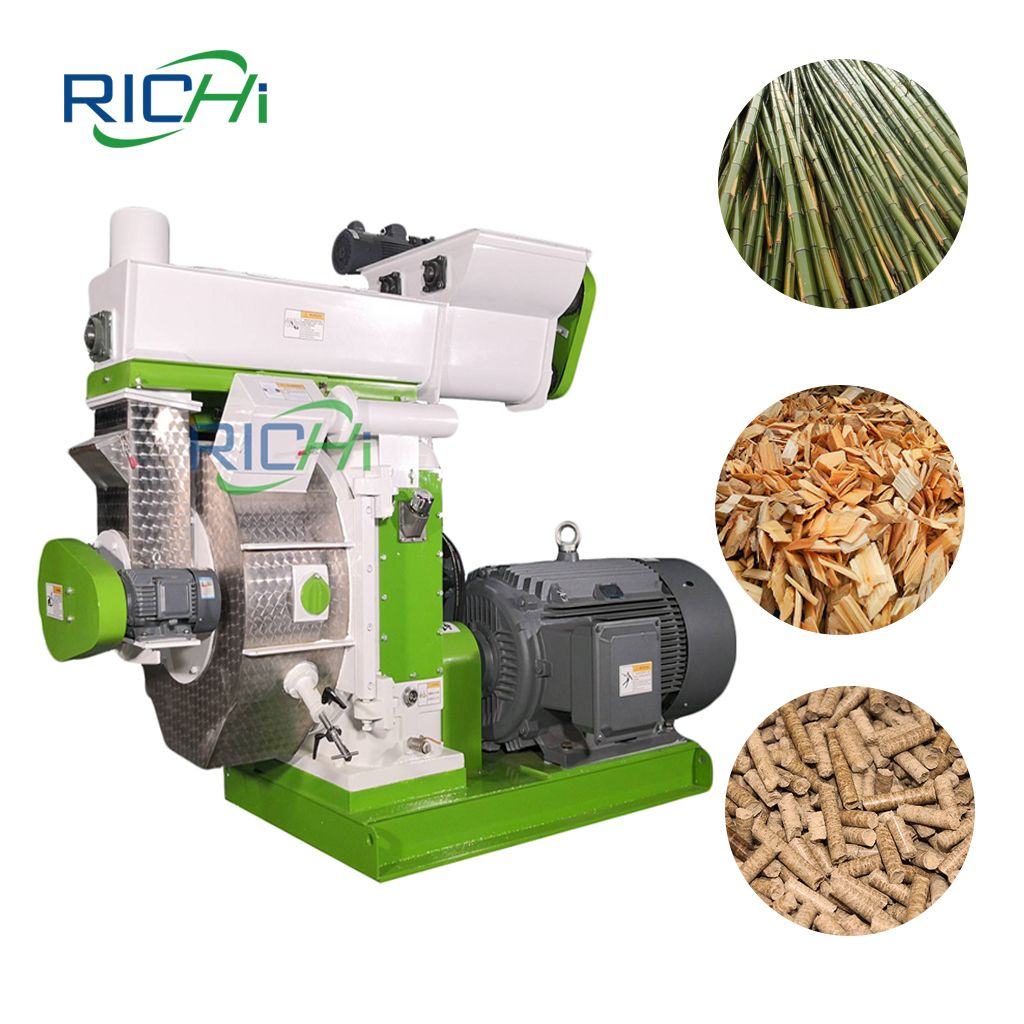
2. The Impact of Feeders on Efficiency
Feeders are essential for controlling the flow of bamboo into the pellet machine. The type and design of the feeder can significantly affect production efficiency.
- Consistent Material Flow: A properly calibrated feeder ensures a consistent flow of raw material into the pellet machine. Inconsistent feeding can lead to fluctuations in production rates and affect pellet quality.
- Type of Feeder: Different types of feeders, such as screw feeders or belt feeders, can be selected based on the material characteristics and desired output. Choosing the right feeder can optimize the feeding process and minimize waste.
3. Importance of Crushers
Crushing bamboo into smaller pieces is a crucial step before pelleting. The efficiency of this process directly impacts the overall production efficiency.
- Particle Size: The size of the crushed bamboo affects how well it binds during pelleting. If the particles are too large, they may not compact properly, leading to lower-quality pellets. Conversely, if they are too fine, it can increase energy consumption and wear on the pellet mill.
- Crusher Selection: Selecting a high-quality crusher that can effectively reduce bamboo to the desired size is essential. A well-designed crusher can improve the efficiency of the entire production line.
4. Conditioning for Optimal Pelleting
Conditioning is a critical process that prepares the bamboo for pelleting by adding moisture and heat.
- Moisture Content: The ideal moisture content for bamboo pellets is typically between 10% and 15%. Proper conditioning ensures that the bamboo fibers are pliable enough to bind together during the pelleting process. Insufficient moisture can lead to weak pellets that break easily.
- Conditioner Design: The design of the conditioner, including its capacity and heating method, can significantly influence production efficiency. A well-designed conditioner that evenly distributes steam or moisture can enhance pellet quality and reduce energy consumption.
5. Cooling Systems and Their Role
After the pellets are formed, they need to be cooled to stabilize their structure and prevent spoilage.
- Cooling Efficiency: Effective cooling systems, such as counterflow coolers, can quickly reduce the temperature of the pellets while minimizing moisture loss. This is crucial for maintaining the integrity of the pellets and ensuring they are ready for packaging.
- Impact on Production Rate: An efficient cooling system can reduce bottlenecks in the production process, allowing for a smoother workflow and higher overall output.
6. Packaging Machines and Final Output
The final step in the production process is packaging the pellets for storage or distribution.
- Automated Packaging: Using automated packaging machines can significantly enhance production efficiency by reducing the time and labor required for packaging. This allows for a quicker turnaround from production to market.
- Quality Control: Proper packaging also plays a role in maintaining pellet quality. Packaging machines that are designed to minimize exposure to moisture and air can help preserve the quality of the pellets during storage.
7. The Importance of Quality Accessories
The quality of the accessories used in a bamboo pellet machine setup can have a profound impact on production efficiency.
- Durability and Reliability: High-quality accessories tend to be more durable and reliable, leading to less downtime and maintenance. This is particularly important in a production environment where consistent output is essential.
- Compatibility and Integration: Accessories that are designed to work seamlessly with the main pellet machine can enhance overall efficiency. Ensuring that all components are compatible can reduce operational issues and improve the production process.
8. Conclusion
The selection of accessories for a bamboo pellet machine is a critical factor that influences production efficiency and the quality of the final product. By carefully choosing feeders, crushers, conditioners, cooling systems, and packaging machines, producers can optimize their production processes, reduce costs, and enhance the overall quality of bamboo pellets. (Related post: Biomass Pellet Press)
Investing in high-quality accessories and ensuring they are properly integrated into the production line will lead to improved operational efficiency and profitability. As the demand for sustainable biomass energy continues to grow, optimizing the production process through thoughtful accessory selection will be essential for maintaining a competitive edge in the market.