Wood pellet machines play a crucial role in converting biomass materials into renewable energy sources. The efficiency, durability, and overall performance of these machines are significantly influenced by the quality and suitability of their accessories. Selecting the right accessories not only enhances the production process but also ensures the long-term reliability and effectiveness of wood pellet machines. This article explores how accessory selection impacts the long-term use of wood pellet machines and provides insights into making informed choices.
1. Understanding the Role of Accessories
Accessories in wood pellet machines include components such as:
- Feeders: Regulate the flow of raw materials into the pellet machine.
- Crushers: Reduce the size of raw materials for optimal processing.
- Conditioners: Add moisture and heat to the raw materials to improve binding.
- Dies and Rollers: Compress the raw materials into pellets.
- Cooling Systems: Cool the pellets after they are formed to maintain their quality.
Each of these accessories plays a vital role in the overall efficiency and longevity of the wood pellet machine.
2. Quality of Feeders
Feeders are essential for ensuring a consistent flow of raw materials into the pellet machine. The quality of the feeder can significantly impact the machine’s performance.
- Durability: High-quality feeders made from durable materials can withstand the abrasive nature of raw biomass. This reduces the frequency of replacements and maintenance, ensuring consistent operation over time.
- Flow Control: A well-designed feeder provides accurate and consistent material flow, preventing fluctuations that can lead to operational issues. Inconsistent feeding can cause pressure variations in the pellet chamber, affecting pellet quality and machine longevity.
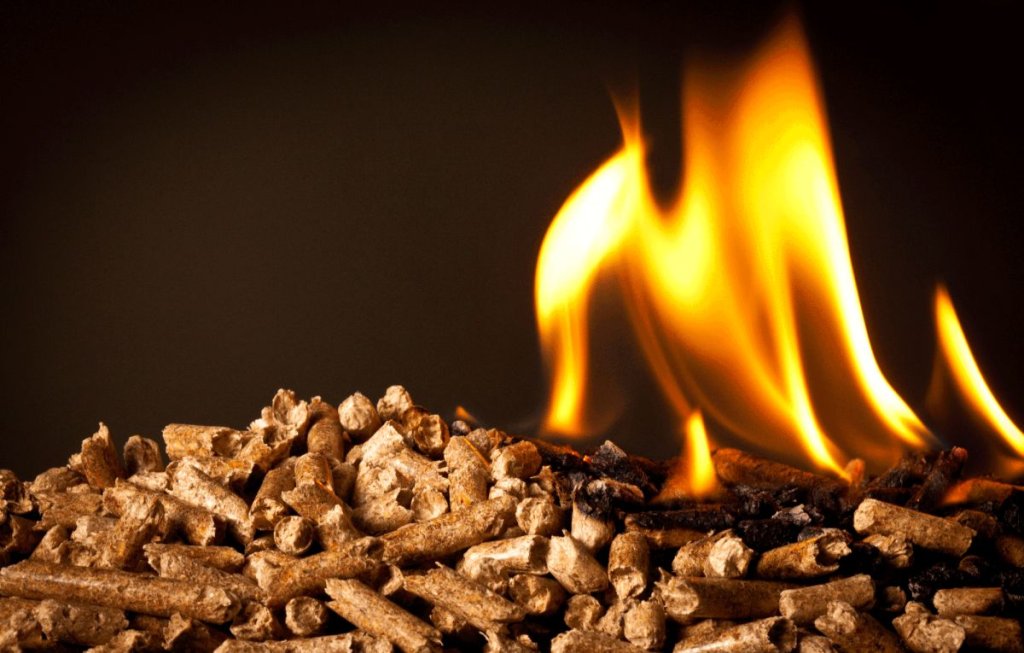
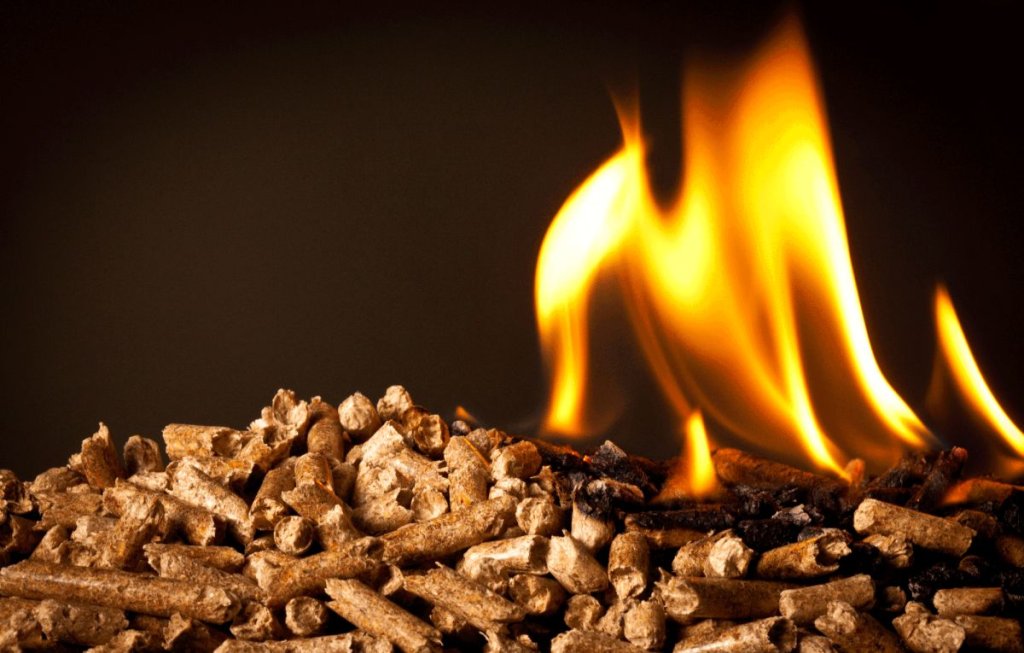
3. Importance of Crushers
Crushers are used to reduce the size of raw materials before they enter the pellet machine. The efficiency and quality of the crushing process are critical for optimal pellet production.
- Particle Size: The right particle size is essential for effective pelleting. If the material is too large, it may not compact properly, leading to weak pellets. Conversely, if it is too fine, it can increase energy consumption and wear on the pellet mill components. Choosing a crusher that can produce the desired particle size consistently is crucial for long-term efficiency.
- Maintenance Needs: Selecting a high-quality crusher with low maintenance requirements can reduce downtime and operational costs. Regular maintenance of the crusher will also prolong its lifespan and ensure consistent performance.
4. Role of Conditioners
Conditioners prepare the raw materials for pelleting by adding moisture and heat. The quality of the conditioning process is vital for producing high-quality pellets.
- Moisture Control: Proper conditioning ensures that the raw materials reach the ideal moisture content for pelleting. If the moisture content is too low, the pellets may break easily; if it is too high, it can lead to poor binding. High-quality conditioners allow for precise control of moisture levels, enhancing pellet quality and machine efficiency.
- Heat Distribution: Effective heat distribution during conditioning helps soften the materials, improving their binding properties. A well-designed conditioner can enhance the overall efficiency of the pellet machine, leading to better long-term performance.
5. Quality of Dies and Rollers
The die and rollers are critical components of the pellet mill, responsible for shaping the pellets. Their quality directly impacts the efficiency and durability of the machine.
- Material Selection: Dies and rollers should be made from high-quality, wear-resistant materials to withstand the high pressures and temperatures during pelleting. Poor-quality components can lead to frequent replacements and increased operational costs.
- Precision Engineering: The precision of the die and roller design is crucial for ensuring consistent pellet size and density. Inaccurate components can lead to uneven pellet formation, affecting the overall quality and performance of the machine.
6. Cooling Systems
Cooling systems are essential for stabilizing the pellets after they are formed. Proper cooling is vital for maintaining pellet quality and preventing spoilage.
- Cooling Efficiency: High-quality cooling systems effectively reduce the temperature of the pellets while minimizing moisture loss. This is crucial for maintaining the structural integrity of the pellets and ensuring they are ready for packaging.
- Impact on Production Rate: An efficient cooling system helps prevent bottlenecks in the production process, allowing for a smoother workflow and higher overall output. This contributes to the long-term viability of the production operation.
7. Selecting Quality Accessories
The selection of high-quality accessories is essential for ensuring the long-term use of wood pellet machines. Here are some considerations for choosing the right accessories:
- Supplier Reputation: Choose accessories from reputable suppliers known for their quality and reliability. Researching suppliers and reading reviews can help ensure that you are investing in durable components.
- Compatibility: Ensure that the accessories are compatible with the specific model of the wood pellet machine. Incompatible components can lead to operational issues and reduced efficiency.
- Warranty and Support: Look for suppliers that offer warranties and after-sales support for their products. This can provide peace of mind and assistance in case of any issues that arise during operation.
8. Conclusion
The selection of accessories for wood pellet extruder machines plays a critical role in determining their long-term performance and efficiency. By focusing on the quality of feeders, crushers, conditioners, dies and rollers, and cooling systems, producers can optimize their pellet production processes and ensure consistent, high-quality output.Investing in high-quality accessories and maintaining them properly will contribute to the overall success and sustainability of wood pellet production operations. As the demand for renewable energy sources continues to grow, prioritizing the selection of quality components will be essential for maintaining a competitive edge in the biomass industry. By understanding the importance of accessory selection, producers can enhance the longevity and efficiency of their wood pellet machines, ultimately leading to greater profitability and sustainability in their operations.