Peanut shell pellet machines are specialized equipment designed to convert peanut shells into high-density pellets, which can be used for energy production or as animal feed. The efficiency and quality of the pellets produced depend significantly on the characteristics of the raw materials used. This article explores the specific requirements of different raw materials for peanut shell pellet machines and how these requirements impact the production process.
1. Peanut Shells as the Primary Raw Material
Peanut shells are the primary raw material for peanut shell pellet machines. Understanding their properties is crucial for optimizing the pelleting process.
- Moisture Content: The ideal moisture content for peanut shells should be between 8% and 15%. If the moisture content is too high, it can lead to poor pellet formation and increased energy consumption during the pelleting process. Conversely, if the moisture content is too low, it may result in weak pellets that break easily. Proper drying equipment may be necessary to achieve the desired moisture levels.
- Particle Size: The size of the peanut shell particles affects how well they bind together during the pelleting process. Ideally, the particle size should be less than 5 mm to ensure uniformity in the pelleting chamber. If the particles are too large, they may not compact properly, leading to lower-quality pellets. Therefore, a reliable crushing system is essential for preparing the raw material.
- Impurities: Peanut shells should be free from foreign materials such as stones, dirt, and other contaminants. Impurities can damage the pellet machine and affect the quality of the final product. A cleaning system should be in place to remove any unwanted materials before the pelleting process begins.
2. Other Agricultural Residues
In addition to peanut shells, other agricultural residues can be mixed with peanut shells to enhance the quality of the pellets.
- Rice Husk: Rice husk is a common additive due to its fibrous nature and availability. It can improve the density and combustion efficiency of the pellets. However, rice husk has a higher silica content, which can lead to wear on the pellet mill components. Therefore, it is essential to monitor the proportion of rice husk used in the mixture.
- Corn Stover: Corn stover, which includes the leaves, stalks, and cobs of corn plants, can also be used in conjunction with peanut shells. It adds bulk to the mixture and can improve the overall energy content of the pellets. The moisture content of corn stover should be managed carefully, as it can vary significantly based on harvesting and storage conditions.
- Wheat Straw: Wheat straw is another agricultural residue that can be blended with peanut shells. It has a low ash content and can enhance the quality of the pellets. The particle size of wheat straw should be reduced to ensure proper mixing and binding during the pelleting process.
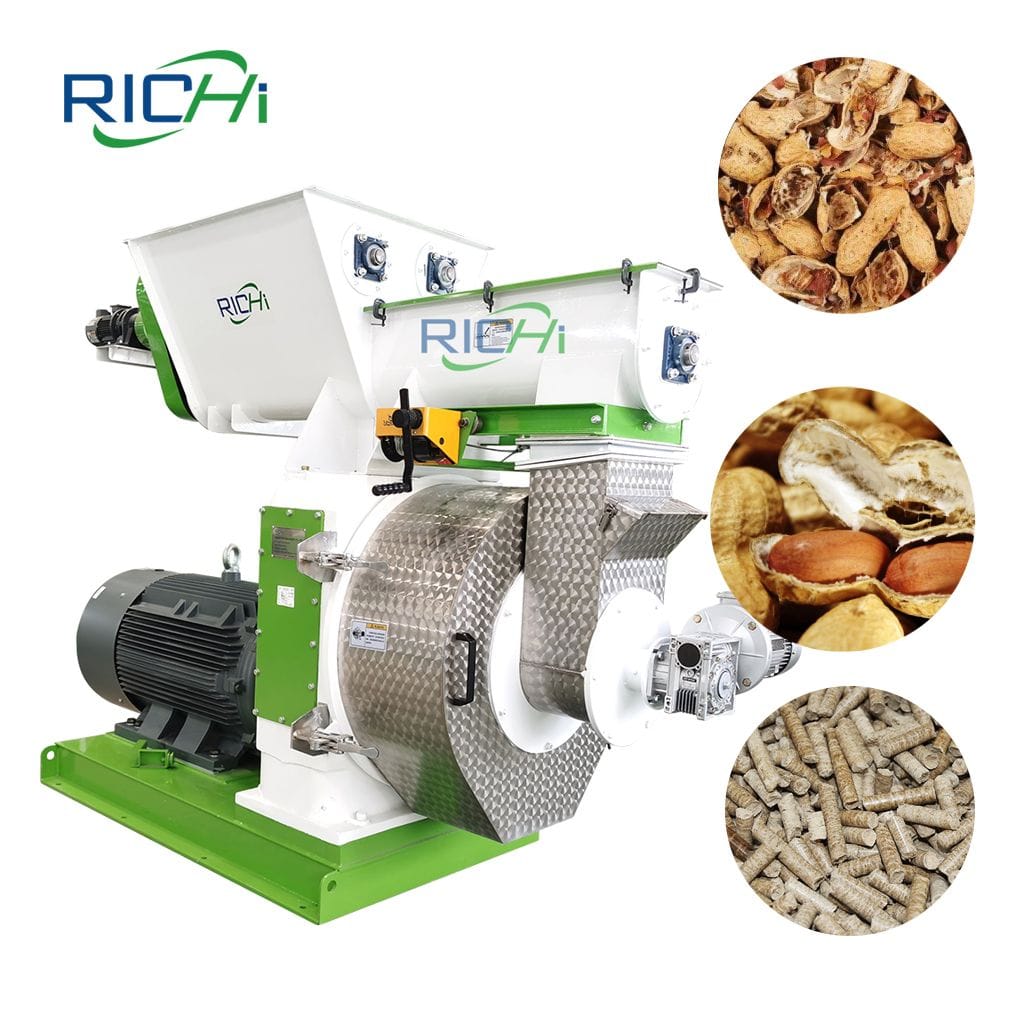
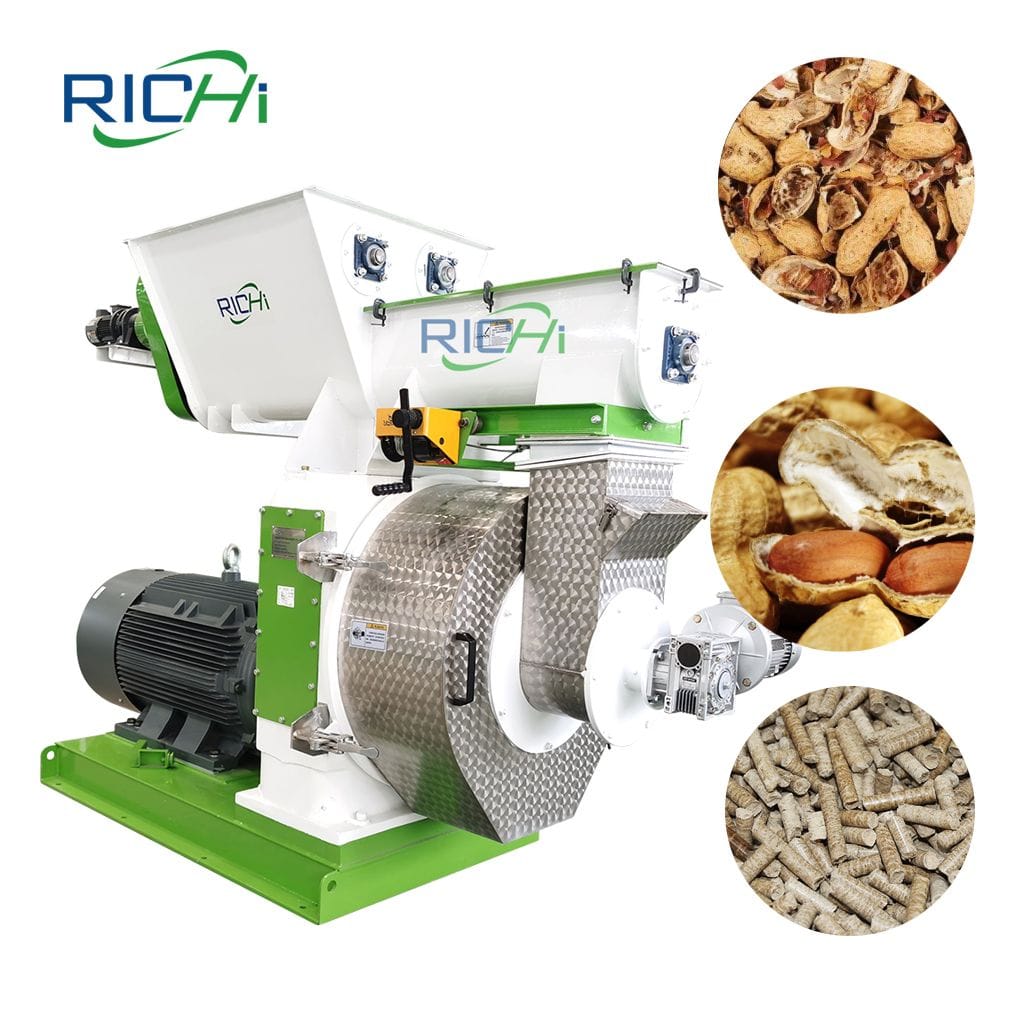
3. Importance of Conditioning
Conditioning is a critical step in the pelleting process that prepares the raw materials for compression.
- Steam Conditioning: Adding steam during the conditioning process helps to soften the fibers of the peanut shells and other materials, improving their binding properties. This process enhances the efficiency of the pellet machine and results in higher-quality pellets. The conditioning temperature should typically range from 70°C to 80°C.
- Moisture Addition: In addition to steam, moisture can be added to the raw materials to achieve the optimal moisture content. However, it is essential to monitor the moisture levels closely, as excessive moisture can lead to poor pellet quality and increased energy consumption.
4. Impact of Raw Material Quality on Pellet Production
The quality of the raw materials used in the pelleting process has a direct impact on the efficiency and effectiveness of the peanut shell pellet machine.
- Combustion Efficiency: Higher-quality raw materials, such as clean and well-prepared peanut shells, result in pellets with better combustion efficiency. The calorific value of the pellets can reach between 3500 and 4000 kcal/kg, making them a viable alternative to traditional fossil fuels.
- Durability and Strength: The durability of the pellets produced is influenced by the quality of the raw materials and the conditioning process. High-quality pellets are less likely to break during handling and transportation, reducing waste and improving profitability.
- Energy Consumption: The choice of raw materials can also affect the energy consumption of the pellet machine. Using well-prepared and appropriately sized materials can lead to lower energy costs during production, enhancing the overall efficiency of the operation.
5. Conclusion
The requirements of different raw materials for peanut shell pellet machines are crucial for optimizing the production process and ensuring high-quality pellets. Managing factors such as moisture content, particle size, and impurities in peanut shells, as well as the use of other agricultural residues, can significantly enhance the efficiency and effectiveness of the pelleting process. (Related post: agriculture pellet machine)
By understanding and addressing these requirements, producers can improve the quality of the pellets, reduce production costs, and enhance the overall profitability of their operations. As the demand for sustainable biomass energy continues to grow, optimizing the use of raw materials in peanut shell pellet production will be essential for maintaining a competitive edge in the market. Investing in high-quality raw materials and effective processing techniques will ultimately contribute to the success and sustainability of the biomass industry.