1. Introduction
In the organic fertilizer production industry, the performance and durability of organic fertilizer pelletizers are crucial for ensuring efficient production and high – quality product output. Key components of pelletizers, such as rollers, dies, screws, and discs, are constantly subjected to wear, corrosion, and high – stress conditions during the granulation process. The use of traditional materials in these components may lead to frequent replacements, increased maintenance costs, and reduced production efficiency. In recent years, with the rapid development of material science, various new materials have emerged, offering great potential for improving the performance of organic fertilizer pelletizers. This article focuses on exploring the application of new materials in the key components of organic fertilizer pelletizers.
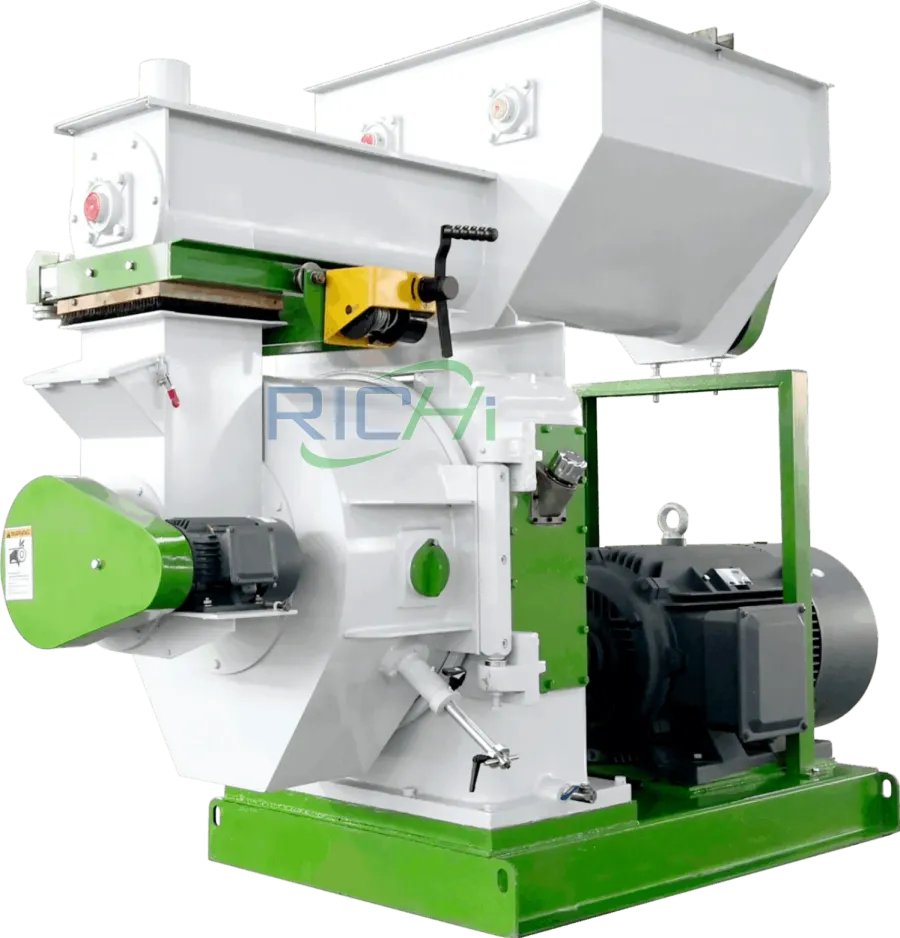
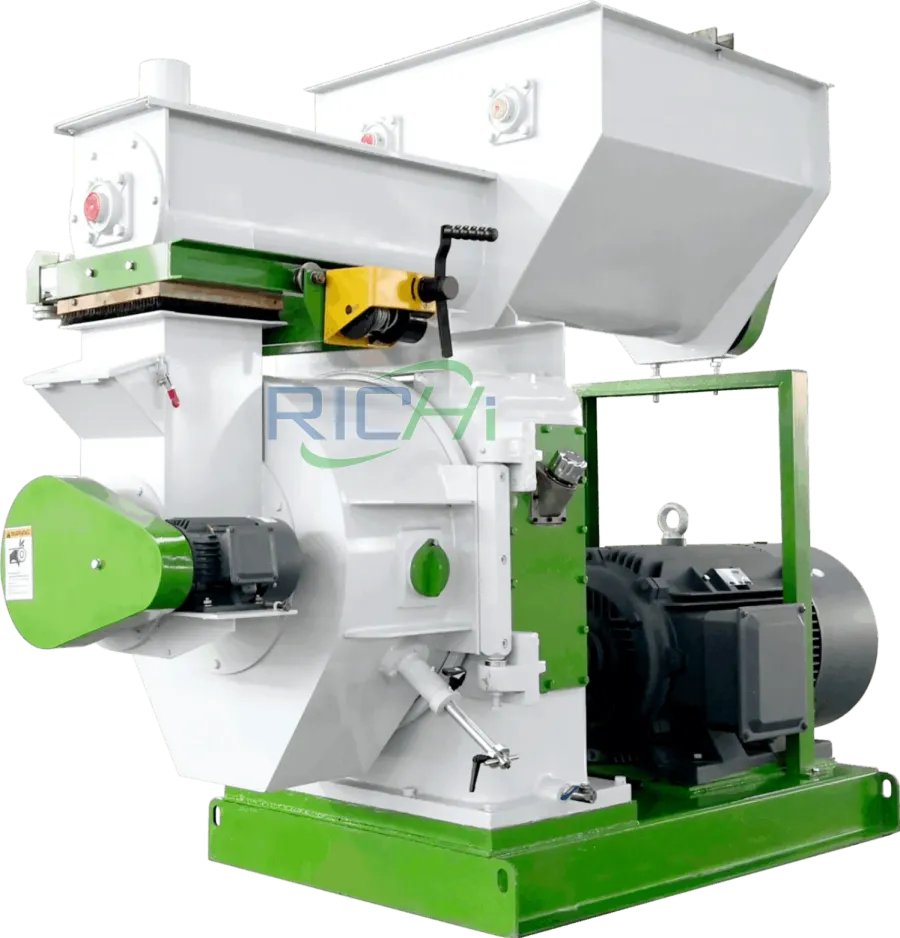
2. Key Components of Organic Fertilizer Pelletizers and Their Working Conditions
2.1 Rollers and Dies in Compression Pelletizers
Rollers and dies are the core components in compression pelletizers. The rollers apply pressure to the organic raw materials, forcing them through the die holes to form pellets. During operation, they are in direct contact with abrasive raw materials, such as compost containing sand – like particles or manure with fibrous substances. The high pressure and friction generated during the compression process cause significant wear on the surface of the rollers and dies. In addition, the presence of moisture and acidic substances in some raw materials can also lead to corrosion problems, reducing the lifespan of these components.
2.2 Screws in Extrusion Pelletizers
Screws in extrusion pelletizers are responsible for pushing the organic raw materials through the die plate. They operate under high – torque conditions and are in continuous contact with the raw materials. The raw materials, especially those with high – viscosity or abrasive properties, can cause severe wear on the screw surface. Moreover, the heat generated during the extrusion process due to friction can also affect the mechanical properties of the screw material, further reducing its service life.
2.3 Discs in Disc Pelletizers
In disc pelletizers, the disc rotates to agglomerate the organic raw materials into pellets. The disc is subjected to the impact and abrasion of the raw materials during rotation. Although the stress on the disc is relatively lower than that on the rollers and screws in other types of pelletizers, long – term operation still causes wear on the disc surface. Additionally, if the raw materials contain corrosive substances, the disc may also be corroded. (Related post: Organic Fertilizer Production Line)
3. New Materials for Key Components of Organic Fertilizer Pelletizers
3.1 Wear – Resistant Alloys
High – Chromium Cast Iron Alloys
High – chromium cast iron alloys are widely used in the manufacturing of rollers and dies in compression pelletizers. These alloys contain a high percentage of chromium, usually between 12 – 30%. Chromium forms hard carbide phases in the alloy matrix, which significantly improves the wear – resistance of the material. The high – chromium cast iron alloys can withstand the abrasive action of organic raw materials for a long time, reducing the frequency of component replacement. For example, compared with traditional carbon – steel rollers and dies, those made of high – chromium cast iron alloys can have a lifespan that is 2 – 3 times longer.
Tungsten – Carbide – Reinforced Alloys
Tungsten – carbide – reinforced alloys are another type of wear – resistant material suitable for key components of fertilizer pellet machines. Tungsten carbide has extremely high hardness and wear – resistance. By embedding tungsten – carbide particles in a metal matrix, such as cobalt – based or nickel – based alloys, the resulting composite material has excellent wear – resistance and toughness. In the case of screws in extrusion pelletizers, using tungsten – carbide – reinforced alloys can effectively reduce wear caused by high – torque and abrasive raw materials, ensuring stable operation of the extrusion process.
3.2 Corrosion – Resistant Materials
Stainless Steels
Stainless steels are commonly used in components that are prone to corrosion, such as in environments where the organic raw materials contain moisture and acidic substances. Austenitic stainless steels, such as 304 and 316 grades, are widely applied. The chromium and nickel content in these stainless steels forms a passive oxide film on the surface, which provides good corrosion resistance. For example, in the production of organic fertilizers from poultry manure, which may contain acidic substances, using stainless – steel discs in disc pelletizers can prevent corrosion and extend the service life of the disc.
Polymer – Coated Metals
Another approach to improving corrosion resistance is to coat metal components with polymers. Polymers such as polyethylene (PE), polypropylene (PP), and polytetrafluoroethylene (PTFE) have excellent chemical resistance. By applying a polymer coating to the surface of metal components, such as rollers and dies, a protective barrier is created between the metal and the corrosive environment. The coating not only resists corrosion but also has a certain degree of lubricity, which can reduce friction and wear. For instance, PTFE – coated dies in compression pelletizers can not only withstand corrosion but also facilitate the extrusion of pellets, improving production efficiency.
3.3 High – Performance Composites
Fiber – Reinforced Composites
Fiber – reinforced composites, such as carbon – fiber – reinforced plastics (CFRP) and glass – fiber – reinforced plastics (GFRP), are increasingly being considered for some components of organic fertilizer pelletizers. These composites offer a combination of high strength, low weight, and good corrosion resistance. In the case of some auxiliary components, such as the housing of pelletizers or certain parts of the feeding system, using fiber – reinforced composites can reduce the overall weight of the equipment, which is beneficial for energy – saving and transportation. Additionally, their corrosion – resistance properties make them suitable for use in harsh production environments.
Metal – Matrix Composites
Metal – matrix composites (MMCs) are also potential materials for key components. MMCs consist of a metal matrix, such as aluminum or magnesium, reinforced with ceramic particles or fibers. For example, aluminum – matrix composites reinforced with silicon carbide (SiC) particles have high strength, good wear – resistance, and lightweight properties. These composites can be used to manufacture components like rollers in compression pelletizers, where their high strength and wear – resistance can improve the performance and lifespan of the equipment. (Related project:6 T/H Fertilizer Manufacturing Plant In Kyrgyzstan)
4. Benefits of Using New Materials in Key Components
4.1 Extended Component Lifespan
The most significant benefit of using new materials in key components is the extension of their lifespan. Wear – resistant alloys and corrosion – resistant materials can effectively reduce the wear and corrosion of components caused by the harsh working conditions in organic fertilizer pelletizers. For example, the use of high – chromium cast iron alloys in rollers and dies can increase their lifespan from several months to over a year in some cases. This not only reduces the frequency of component replacement but also minimizes production downtime, ensuring continuous and stable production.
4.2 Improved Production Efficiency
New materials can also contribute to improved production efficiency. Components made of wear – and corrosion – resistant materials can maintain their optimal performance for a longer time. For instance, screws made of tungsten – carbide – reinforced alloys can operate smoothly without significant wear, ensuring a stable extrusion speed in extrusion pelletizers. In addition, some lightweight composite materials can reduce the energy consumption of the equipment, further improving production efficiency.
4.3 Enhanced Product Quality
The use of new materials in key components can have a positive impact on the quality of the granulated organic fertilizers. For example, smooth – surfaced and wear – resistant dies made of new materials can produce pellets with more uniform shapes and sizes. Components that are resistant to corrosion can prevent the contamination of the organic fertilizers by metal ions from corroded parts, ensuring the purity and quality of the product.
5. Challenges and Solutions in Applying New Materials
5.1 High Cost of New Materials
One of the main challenges in applying new materials in organic fertilizer pelletizers is their relatively high cost. Wear – resistant alloys, high – performance composites, and some corrosion – resistant materials are more expensive than traditional materials. To address this issue, manufacturers can consider several solutions. First, they can optimize the design of components to reduce the amount of material used while still maintaining the required performance. Second, through large – scale production and bulk purchasing of new materials, economies of scale can be achieved, reducing the unit cost. Third, research and development efforts can be focused on finding more cost – effective new materials or improving the manufacturing processes of existing new materials to lower production costs.
5.2 Compatibility with Existing Equipment and Processes
Another challenge is ensuring the compatibility of new materials with existing equipment and production processes. New materials may have different mechanical properties, such as hardness, elasticity, and thermal conductivity, compared to traditional materials. This may require adjustments to the manufacturing and assembly processes of components. For example, when using high – hardness wear – resistant alloys to manufacture rollers, the machining process may need to be optimized, and new cutting tools may be required. To solve this problem, close cooperation between material suppliers, equipment manufacturers, and end – users is necessary. Material suppliers can provide technical support on the processing and application of new materials, and equipment manufacturers can make appropriate modifications to the equipment design and production processes.
6. Case Studies of New – Material Applications
6.1 Case 1: A Medium – Sized Organic Fertilizer Plant
A medium – sized organic fertilizer plant replaced the traditional carbon – steel rollers and dies in its compression pelletizers with high – chromium cast iron alloys. Before the replacement, the rollers and dies needed to be replaced every 3 – 4 months due to severe wear. After using the high – chromium cast iron alloys, the lifespan of the rollers and dies increased to 8 – 10 months. The production downtime caused by component replacement was significantly reduced, and the production capacity of the pelletizers also increased by about 15% due to the more stable operation of the equipment.
6.2 Case 2: A Small – Scale Extrusion – Pelletizer – Using Organic Fertilizer Manufacturer
A small – scale organic fertilizer manufacturer using extrusion pelletizers faced problems with screw wear. The original carbon – steel screws needed to be replaced every 2 – 3 months. After switching to screws made of tungsten – carbide – reinforced alloys, the lifespan of the screws extended to 6 – 8 months. In addition, the extrusion process became more stable, and the quality of the extruded pellets improved, with more uniform particle sizes and higher density.
7. Conclusion
In conclusion, the application of new materials in the key components of organic fertilizer pelletizers has great potential to improve the performance, lifespan, and production efficiency of the equipment. Wear – resistant alloys, corrosion – resistant materials, and high – performance composites offer various advantages in different aspects. However, challenges such as high material costs and compatibility issues need to be addressed. Through continuous research and development, cost – reduction measures, and close cooperation among relevant parties, new materials will play an increasingly important role in the development of organic fertilizer pelletizers, promoting the sustainable development of the organic fertilizer production industry.