When using a ring die pellet maker to compress timber pellets, we commonly come across the sensation of obstruction of the ring die openings. When the mold opening is obstructed, not only is the moment required to take apart and also cleanse the mold, however likewise the manufacturing effectiveness is impacted by the failure to produce particles after the mold is obstructed.
How to stay clear of obstruction of ring die opening of pellet maker? In today’s write-up, we will evaluate some of one of the most common causes and also just how to address the trouble after the pellet maker mold is blocked.
How to stay clear of blockage of ring die opening of pellet maker?
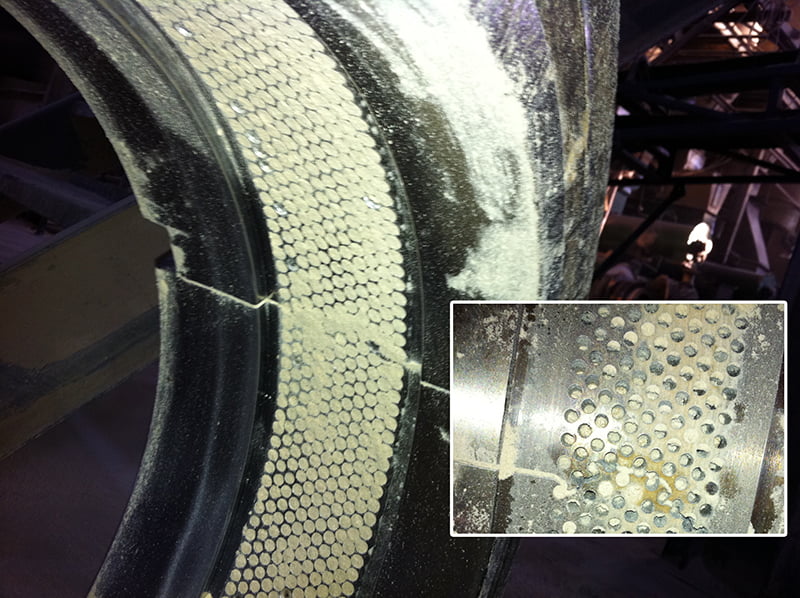
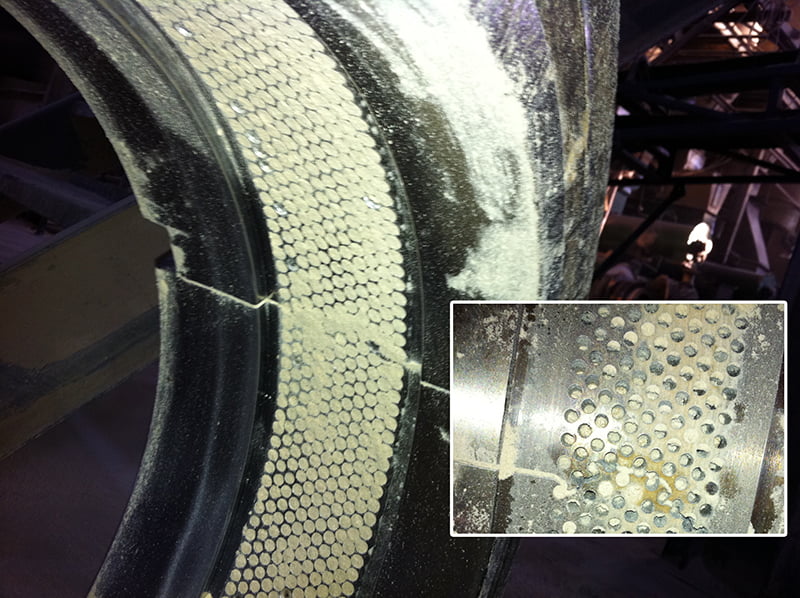
1. The pellet machine mold and mildew needs to be polished. The cause of the clog of the brand-new ring die is different from that of the old one. Some new molds will have defects in the mold opening throughout the exploration process.
The internal surface of the hole may appear smooth. Nevertheless, generally the drilling process likewise generates small scrapes. Even these little scrapes will generate adequate resistance during the manufacture of bits, resulting in mold.
Head blocked. Bear in mind that if the rollers of the pellet equipment can not create sufficient pressure to get over the resistance of the die openings, it will certainly cause clog. Typically utilize a fairly loose biomass material (I like to make use of wheat bran), concerning 10-15% grease as well as about 1-2% fine sand.
You blend this material thoroughly, and then gradually and consistently process it in a pellet equipment. This polishing product will certainly aid clean the surface area of the mold opening and also eliminate rust.
Expert suggestion: Use much less polishing materials. If the frequency of use is too high, the surface area of the mold and mildew and the stress roller will certainly be put on, therefore shortening its service life. When the material guide on the mold is worn, the compression proportion on the mold will not be suitable for producing top notch pellets.
2. Raw material granularity. Make certain that the fragment size of the raw material is smaller than the size of the die opening. As an example, a ring die with an aperture of 6mm utilizes a 5mm hammer mill screen to generate 6mm wood pellets.
Professional idea: It is likewise required to ensure that there is no contamination in the raw products (stone/metal). These will not just create obstruction of the die openings, but also create severe damage to the pellet equipment itself. This may include damages to the transmission or motor.
3. Raw material moisture. It is extremely vital to control the moisture material of the raw material when making timber pellets. The perfect wetness content of the raw material is less than 15%. If the dampness content is too high, such as 20%+, it will quickly create bits when it gets in the pellet machine. The mold hole is obstructed.
Professional tip: Even if you prepare raw materials with perfect bit size and moisture material, you should likewise take into consideration utilizing granular binders. Fragment binders can aid the procedure as well as lower the opportunity of clogging of the pellet machine die.
4. It is advised to feed the pellet machine gradually to avoid clog of the mold. When the pellet equipment functions, there will be a specific temperature level, when it exceeds 80 degrees Celsius, the all-natural lignin in the timber will certainly melt and bind the pellets with each other.
Nevertheless, if the raw material of the pellet maker is fed into the mold and mildew faster than the processing speed of the raw product, it is very easy to block the mold prior to the pellet maker reaches this operating temperature. You have to make sure that there suffices product before the granulation area, however do not entirely cover them.
Specialist idea: The pellet manufacturing process generates warm, which launches the dampness in the raw product. Loading the pellet maker processing chamber with raw materials stops the retreat of moisture (vapor). This steam is then taken in by the incoming raw materials. This suggests that raw materials with dampness greater than 15% can cause die blockage. Therefore, only feed the pelletizer at a rate that can be refined.
5. If you have actually ended up making timber pellets, add a big amount of grease to the blend in the last couple of mins of the procedure. This will certainly leave a soft oily product in the mold and mildew, which will certainly make it easier to begin making pellets again following time.