Friends who plan to engage in organic fertilizer production must be most concerned about how much is a set of organic fertilizer production line equipment? In fact, it is not difficult to determine this problem, as long as the production process and annual output of organic fertilizer are determined, the price range can be roughly determined.
In fact, the use combination of organic fertilizer production line equipment is mainly related to production raw materials, production process, annual output, etc. The specific design and combination still need specific communication.
1. How to choose and match fertilizer pellet machine line?
(1) Determine the output size of the fertilizer pellet machine production line: For example, if the annual output is many tons, or many tons per hour, the price can be determined. The models of the complete sets of fertilizer pellet machine of normal organic fertilizer equipment manufacturers are divided into several models with an annual output of 1, 2, 3, 4, 5, and 100,000 tons.
(2) Determine the shape of the pellets: powder, column, oblate or standard round. Commonly used granulation equipment are: disc granulator, drum organic fertilizer pellet making machine, roller extrusion organic fertilizer pellet making machine, flat die organic fertilizer pellet making machine, ring film granulator. The selection of the granulator should be based on the local fertilizer market conditions.
(3) Determine the fertilizer pellet plant equipment: the fertilizer pellet machine is different, the price of the fertilizer pellet machine is different, and the amount of labor is different:
⑷ Determine the type of fertilizer produced. There are 4 types of popular organic fertilizers, pure organic fertilizer, organic-inorganic compound fertilizer, bio-organic fertilizer, compound microbial fertilizer.
⑤Selection of fermentation turning and throwing machine: The popular fermentation methods include stack fermentation, shallow water fermentation, deep tank fermentation, tower fermentation, and rotary drum fermentation. The fermentation methods are different, and the fermentation equipment is also different.
⑥Determine the types of primary organic fertilizer raw materials: the common organic raw materials are chicken manure, pig manure, cow manure, sheep manure, straw, medicinal residue, furfural residue, humic acid, pond mud, and living and livelihood pollution from urban sewage treatment plants, etc.
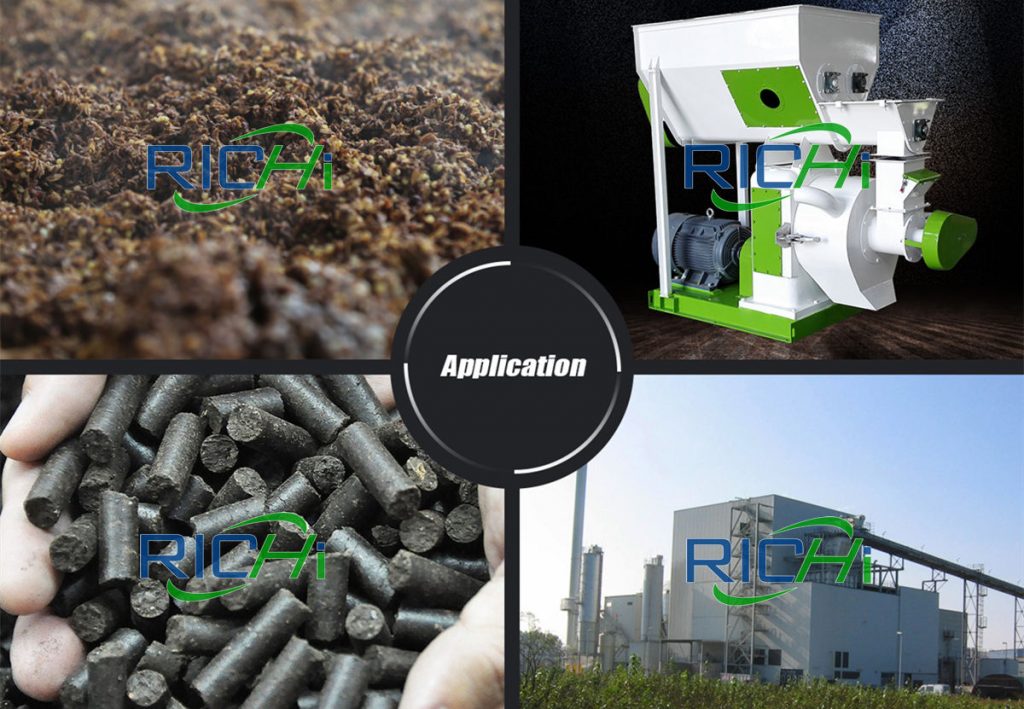
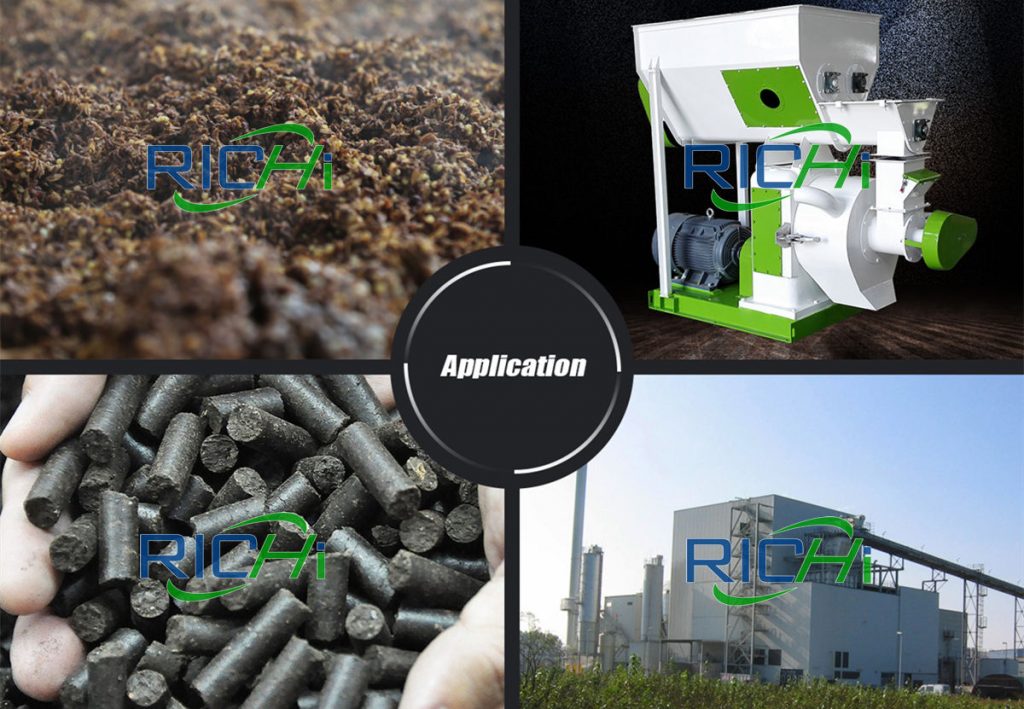
2. Production process of fertilizer pellet machine production line
The 8 processes of the organic fertilizer production line are introduced, namely: batching, crushing, stirring, granulation, drying, screening, cooling, and packaging.
(1) Ingredients
The device adopts 5 measuring belt scales, and the computer controls the feeding amount and ratio. The operator only needs to put the powdered organic raw materials (after the fermentation is completed), NPK, additives, trace elements, etc. into the hopper of the metering belt, and the feeding port of the hopper is flush with the ground, which can not only reduce the labor intensity of the workers, but also reduce the The secondary conveying process of raw materials, and the uniform entry of materials into the fertilizer pellet machine stabilizes the granulation state, thus improving the spheroidization rate to a certain extent and reducing the production cost.
(2) Broken
The semi-wet material pulverizer is used in this process. The semi-wet material pulverizer can crush the bulk materials in the raw material, and has the advantages of good working performance, strong continuity and easy dust removal, which improves the working environment of the fertilizer pellet machine.
The wet material pulverizer is also called coal gangue pulverizer and ore pulverizer, which is used to pulverize various minerals. The problems of material blocking, sticking, and easy burning of the motor in the actual use of the traditional wet material pulverizer are improved.
The internal structure of the latest wet material pulverizer has been greatly improved, which completely solves a series of problems that are difficult to solve in the production process of the wet material pulverizer. The biggest difference from the previous generation of wet material pulverizers is: low price, high efficiency, and improved feeding port.
The wet material pulverizer improved by this method has a smoother feeding, and will not stick to the hammer and the inner wall due to the wet sticking of the material, which ensures the smooth production of the pulverizing workshop in the fertilizer pellet machine production line and delivers high-quality raw materials for the next fertilizer pellet machine production process.
Semi-wet material crusher is a new type of high-efficiency single-rotor reversible crusher. The semi-wet material pulverizer has strong adaptability to the moisture content of the material, especially for the fermented decomposed waste or other materials with a moisture content of ≤30%, which can be used for milling, and the milling particle size can reach 20~30 mesh. Feed particle size requirements for general fertilizer pellet machine.
This machine shortens the process flow for fertilizer pellet machine and compost production, reduces equipment investment, and saves operating costs. It is an ideal machine for fertilizer production and processing units.
(3) Stirring
The selection of mixing equipment in the fertilizer pellet machine production line is also crucial. The mixing degree of raw materials determines the quality of granulation. At present, the main mixing equipment in the industry include heavy-duty disc mixers, horizontal mixers, double-shaft high-power mixers, and vertical mixers.
There are various options, and the configuration machines for different output options are different. Generally, the production of organic fertilizer with an annual output of 5000-20000 tons generally uses a horizontal mixer. The advantages of the horizontal mixer are high mixing uniformity, high production efficiency, extremely low failure rate, etc., and the residual amount is small.
It is suitable for mixing and mixing, organic fertilizer ingredients, and additive premixes. mix. Therefore, the mixing uniformity is improved, and the novel rotor structure is adopted, and the minimum gap between the rotor and the casing can be adjusted to close to zero, which effectively reduces the residual material in the machine.
(4) Granulation
The choice of fertilizer pellet machine is very important in the production of organic fertilizer. At present, there are many methods in the industry, such as disc, rotating drum, stirring drum, extrusion, etc. Each of these methods has its own advantages and disadvantages.
The advantages of the disc fertilizer pellet machine are intuitive operation, simple control, high spheroidization rate, less material return, fewer equipment wearing parts, and less maintenance; the disadvantage is that the single fertilizer pellet machine has a small processing capacity and insufficient particle strength. In consideration of appearance quality, energy saving and other aspects, this process selects two disc fertilizer pellet machines and sets them in parallel.
(5) Drying
Although most of the granulated materials have been formed into granules, at this time, the granules have high moisture content and low strength, which cannot meet the requirements of packaging and transportation, and must be dried.
Considering that the moisture content of the material in this system is high during granulation, and the finished product requires low moisture content, limited by the nature of the material, the strength of the particles coming out of the fertilizer pellet machine is small, and the damage of the particles must be minimized during the drying process.
Large diameter dryers were chosen, so the system was equipped with two rotary dryers. In the downstream drying process, only the material is intensively dried at medium temperature, so as to avoid the material temperature being too high when the material is discharged, which will increase the load of the cooler and affect the cooling effect.
(6) Screening
After drying, there are powdery materials and large pellets. The large particles are all screened out by the sieving machine. The large particles are crushed by the pulverizer and the fine powder is directly returned to the fertilizer pellet machine through the return belt conveyor to be mixed with the raw materials. In this way, a complete production cycle is formed, and the finished product enters the cooling process.
(7) Cooling
Through the cooling treatment of the rotary cooler, the pellete strength is further improved and the moisture content is reduced. During the cooling process, due to the friction between the material and the cylinder wall and the copying plate, fine powder will inevitably be generated, so the rear end of the cooler is increased.
A trommel screen is used to screen out fine powder to ensure the quality of the finished product. This section of the process has very little fine powder and is processed manually.
(8) Packaging
Qualified finished products from fertilizer pellet machine are packaged by automatic packaging machine, which automatically weighs, unloads, sews packages, measures accurately, and is easy to operate, which improves work efficiency again.
The material is added to the weighing hopper by the feeding mechanism (pneumatic gate). After the controller receives the weight signal from the sensor, it will be controlled according to the preset program value.
When the weight is greater than or equal to (target value-coarse metering value), stop the fast feed signal output, and enter into medium-speed (middle and slow adding at the same time) feeding; when the weight is greater than or equal to (target value-fine metering value) When the weight is greater than or equal to (target value – overshoot value), stop the slow-feeding signal output, the feeding door is completely closed, and the fixed value is weighed.
3.Floor area of fertilizer pellet machine line
The floor area of fertilizer pellet machine production line is mainly related to the annual output, and is generally divided into the following types:
- An organic fertilizer processing plant with an annual output of 5,000 tons requires 1,000-1,500 square meters;
- An fertilizer pellet machine plant with an annual output of 10,000 tons requires 1500-2000 square meters;
- An organic fertilizer processing plant with an annual output of 20,000 tons requires 2000-2500 square meters;
- An organic fertilizer processing plant with an annual output of 30,000 tons requires 3,000-3,500 square meters;
- An fertilizer pellet machine processing plant with an annual output of 50,000 tons requires 5,000-6,000 square meters.