Organic fertilizer pellet machines are vital for transforming raw organic materials into uniform, easy-to-use pellets. To ensure efficient operation and high-quality output, several key technical parameters must be carefully monitored and controlled throughout the production process. This article highlights the critical technical indicators operators should focus on when using organic fertilizer pellet machines.
Moisture Content
Moisture content is one of the most crucial factors in the pelletization process:
- Optimal Range: The ideal moisture content for most organic materials lies between 13-18%.
- Monitoring: Regularly use moisture meters to check the raw material and make necessary adjustments.
- Impact: Insufficient moisture can lead to poor binding and dusty pellets, while excessive moisture can clog the machine and result in low-quality pellets.
Particle Size
The size of the raw material particles significantly influences the pelletization process:
- Recommended Size: Particles should typically be between 2-5 mm for optimal pellet formation.
- Consistency: Ensure a uniform particle size distribution for consistent pellet quality.
- Monitoring: Regularly assess the output of grinding equipment and adjust as needed.
Die Temperature
The temperature of the die during pelletization is critical:
- Optimal Range: Typically maintained between 60-90°C (140-194°F), depending on the material.
- Monitoring: Utilize infrared thermometers or built-in temperature sensors.
- Impact: Maintaining the proper die temperature ensures effective pellet formation and minimizes wear on the machine.
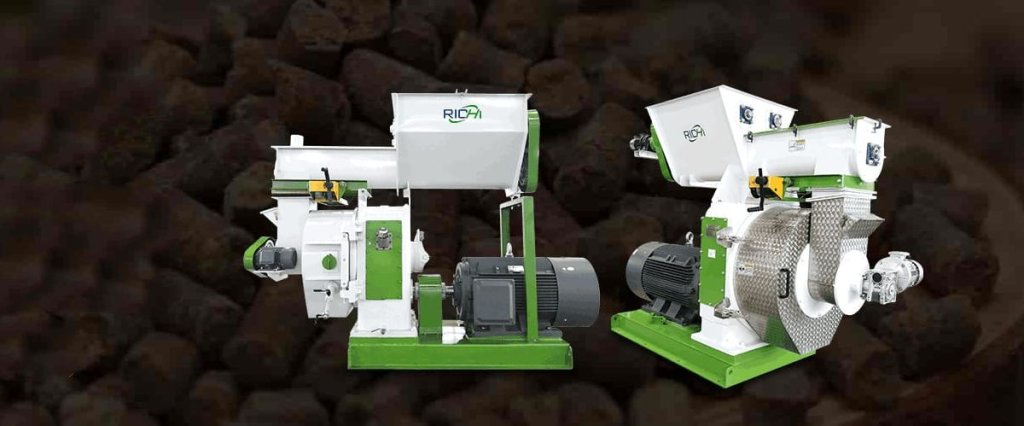
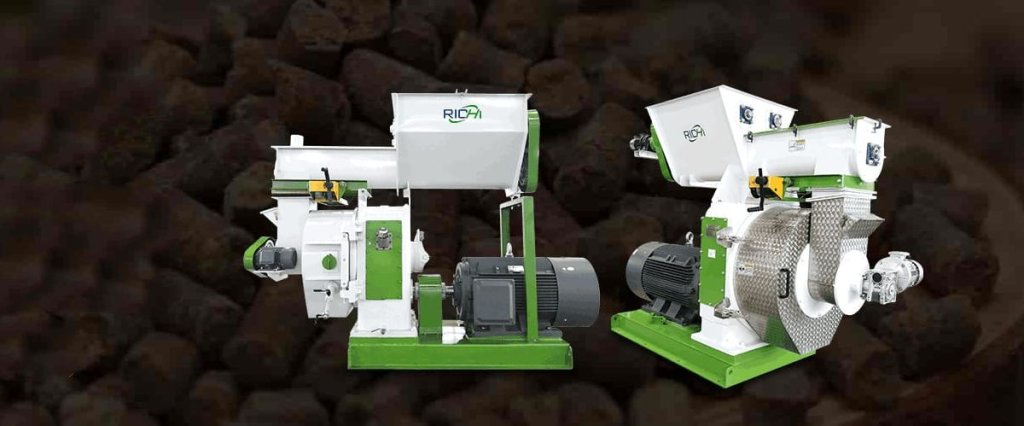
Compression Ratio
The compression ratio of the die affects pellet density and durability:
- Typical Range: Generally between 1:6 to 1:8, depending on the material and desired pellet characteristics.
- Adjustment: Can be modified by changing die thickness or hole diameter.
- Impact: Higher compression ratios typically produce denser, more durable pellets but require increased energy.
Pellet Density
The density of the produced pellets serves as a key quality indicator:
- Target Range: Usually between 600-700 kg/m³ for most organic fertilizers.
- Measurement: Employ a density meter or the displacement method to check pellet density.
- Significance: Proper density ensures good handling characteristics and consistent nutrient content per volume.
Pellet Durability Index (PDI)
PDI assesses the pellet’s ability to withstand handling without breaking:
- Acceptable Range: A PDI above 95% is generally considered good for organic fertilizer pellets.
- Testing: Regularly measure PDI using a pellet durability tester.
- Importance: High durability reduces dust formation and ensures pellets remain intact during transport and application.
Production Capacity
Monitoring the actual production rate against the machine’s rated capacity is essential:
- Measurement: Track output in kg/h or t/h.
- Optimization: Adjust feed rate, die speed, and other parameters to maximize production while maintaining quality.
- Efficiency: Compare actual output to rated capacity to identify potential issues or inefficiencies.
Energy Consumption
Energy efficiency is critical for managing operational costs and promoting sustainability:
- Measurement: Monitor kWh consumed per ton of pellets produced.
- Benchmarking: Compare energy consumption to industry standards or previous performance.
- Optimization: Adjust machine parameters to minimize energy use while maintaining product quality.
Raw Material Feed Rate
Controlling the feed rate is crucial for consistent pellet quality:
- Adjustment: Match the feed rate to the machine’s capacity and the material’s characteristics.
- Monitoring: Use weight sensors or flow meters to ensure consistent feeding.
- Impact: An appropriate feed rate ensures uniform pellet formation and prevents machine overloading.
Cooling Temperature
The temperature of pellets after extrusion and cooling is significant:
- Target: Pellets should be cooled to within 5°C of ambient temperature.
- Monitoring: Use temperature probes at the cooler outlet.
- Significance: Proper cooling ensures pellet stability and prevents moisture condensation during storage.
Nutrient Content
While not a direct machine parameter, monitoring the nutrient content of the pellets is vital:
- Testing: Regularly analyze N-P-K content and other relevant nutrients.
- Consistency: Ensure nutrient levels meet specified ranges for the product.
- Adjustment: Modify the raw material mix if nutrient content deviates from targets.
Pellet Size and Shape
Consistency in pellet size and shape is important for quality control:
- Measurement: Regularly check pellet diameter and length.
- Uniformity: Aim for consistent size and a cylindrical shape.
- Adjustment: Fine-tune die specifications if pellet size or shape deviates from standards.
Conclusion
Monitoring and controlling these key technical parameters are essential for the efficient operation of organic fertilizer pellet machines and the production of high-quality pellets. Regular checks, adjustments, and maintenance based on these indicators will optimize the pelletization process, reduce operational issues, and ensure consistent product quality.
Operators should establish a routine monitoring schedule for these parameters and maintain detailed records. This data can be invaluable for troubleshooting issues, optimizing production, and ensuring consistent quality over time. As technology advances, many modern pellet machines incorporate sensors and automated control systems to monitor and adjust these parameters in real time, further enhancing efficiency and product consistency.
By paying close attention to these key technical indicators, manufacturers can maximize the performance of their organic fertilizer pellet machines, produce high-quality pellets, and meet the growing demand for organic fertilizers in agriculture and horticulture. (Related post: compost pelleting machine)