Sinking fish feed pellet mills are widely used in the aquaculture sector to produce high-quality fish feed. However, to attain optimum efficiency and productivity, it is essential to understand how to effectively run and preserve the pellet mill. In this essay, we will discuss some functional ideas on how to optimize the efficiency of your sinking fish feed pellet mill.
1. Select the Right Raw Materials
The quality of the raw materials utilized in fish feed manufacturing has a significant impact on the efficiency of the pellet mill. It is essential to pick high-quality raw materials that are appropriate for the type of fish being fed. As an example, fish meal is a typical component utilized in fish feed manufacturing, however not all fish meals are produced equal. Picking a top notch fish meal that is rich in protein and low in ash material can improve the efficiency of the pellet mill and the quality of the fish feed produced.
2. Proper Conditioning of Raw Materials
Conditioning is the procedure of including vapor and water to the raw materials to raise their moisture content and enhance their flowability. Proper conditioning of the raw materials is vital to the efficiency of the pellet mill. If the raw materials are too dry, they will certainly not move smoothly through the pellet mill, which can result in uneven pellet size and low manufacturing efficiency. On the other hand, if the raw materials are too wet, they can block the pellet mill and decrease its efficiency. Therefore, it is essential to discover the right equilibrium of moisture web content through proper conditioning.
3. Regular Maintenance
Regular maintenance of the sinking fish feed pellet mill is critical to its efficiency and durability. Proper maintenance consists of cleansing and oiling the machine regularly, replacing worn or damaged parts, and checking the maker for indicators of wear and tear. A poorly kept pellet mill will certainly operate much less effectively, which can bring about lowered performance, enhanced energy prices, and even maker breakdowns.
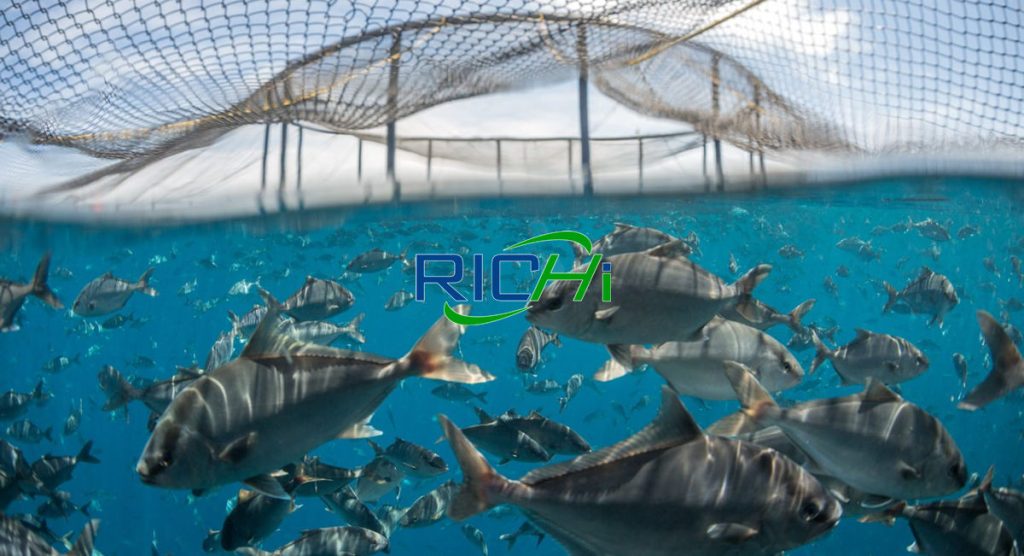
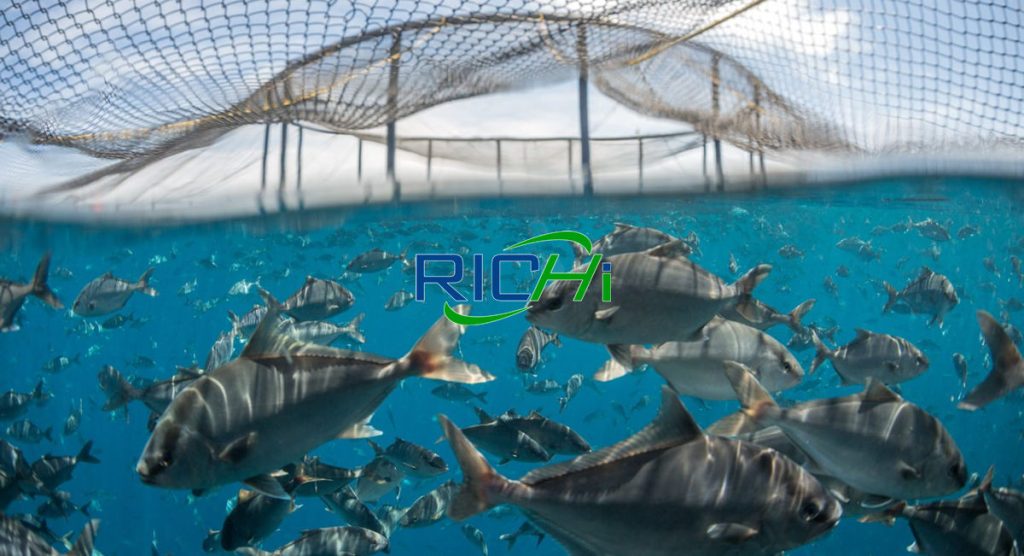
4. Adjusting the Die and Roller Gap
The die and roller gap is the range in between the die and the roller, which establishes the size of the pellets produced. It is essential to adjust the die and roller gap appropriately to optimize the efficiency of the pellet mill. If the gap is too large, the pellets will be too huge, resulting in reduced manufacturing efficiency and lower high quality pellets. On the other hand, if the gap is too narrow, the machine will certainly be overloaded, leading to lowered performance and increased wear and tear on the machine.
5. Controlling the Pellet Mill Temperature
Controlling the temperature of the pellet mill is necessary for optimizing its efficiency. The ideal temperature variety for the pellet mill is between 70 and 80 degrees Celsius. If the temperature is too low, the pellets will certainly be too soft and will not hold their shape, resulting in lower top quality pellets. On the other hand, if the temperature is too expensive, the pellets will certainly come to be brittle and disintegrate conveniently, which can additionally lead to reduced high quality pellets. Therefore, it is important to preserve the appropriate temperature to produce high-grade pellets efficiently.
6. Monitoring the Feed Rate
The feed rate is the rate at which the raw materials are fed right into the pellet mill. Monitoring the feed rate is important to make sure that the pellet mill is performing at its optimum efficiency. If the feed rate is too sluggish, the equipment will certainly be underutilized, resulting in reduced production efficiency. On the other hand, if the feed rate is too quick, the maker will certainly be overloaded, leading to decreased manufacturing efficiency and raised wear and tear on the maker.
7. Using a Proper Pellet Binder
A pellet binder is a substance that is included in the raw materials to help them stick during the pelletizing procedure. Using a proper pellet binder is essential for optimizing the efficiency of the pellet mill. A premium binder will assist the pellets hold their shape and prevent them from damaging.